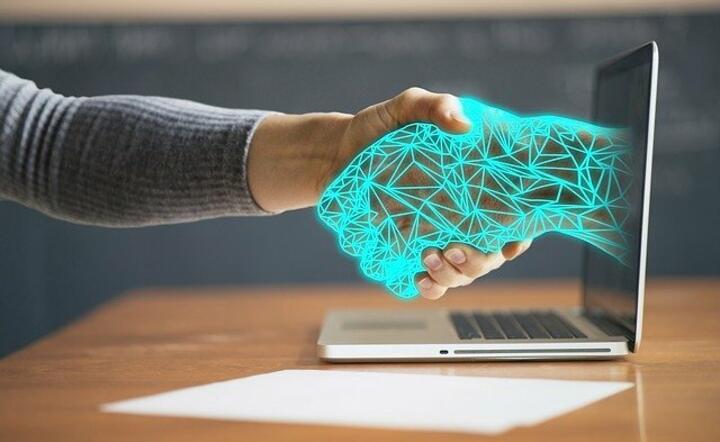
Robota pilnie zatrudnię!
Nowe systemy stają się coraz atrakcyjniejsze, także dzięki planowanej przez Ministerstwo Rozwoju, Pracy i Technologii uldze na automatyzację i robotyzację. Tego właśnie potrzebuje polski przemysł
Polska gospodarka wyraźnie odbiła po związanych z pandemią spadkach. Według tzw. szybkiego szacunku GUS, w drugim kwartale 2021 r. tempo rozwoju gospodarczego wyniosło rekordowe 10,9 proc. r/r. Jednocześnie indeks PMI, obrazujący kondycję przemysłu, po rekordowym wyniku na poziomie 59,4 proc. w czerwcu, w lipcu wciąż wskazywał na bardzo dobre warunki w ramach całego sektora i szybkie tempo wzrostu w stosunku do danych historycznych . Aby trend wzrostowy utrzymał się na dłużej, potrzebna jest jednak daleko idąca cyfryzacja i robotyzacja polskiego przemysłu.
Poszczególni przedstawiciele sektora produkcji rozwijają poziom wykorzystania technologii w różnym tempie. Niektóre klasyczne gałęzie przemysłu przetwórczego i wydobywczego, takie jak przemysł naftowy, metalurgiczny, węglowy, papierniczy czy tytoniowy, modernizują systemy automatyzacji w sposób bardzo zachowawczy. Inne, do których należą: chemia specjalistyczna, branża farmaceutyczna, żywność i napoje oraz inne towary szybko zbywalne, przyspieszają swoją ekspansję, zwracając się ku inteligentnym metodom produkcji, które pomogą sprostać gwałtownemu wzrostowi.
Optymalne kosztowo procesy inteligentnej produkcji oraz planowana ulga na robotyzację i automatyzację tworzą nowe możliwości dla firm produkcyjnych w zakresie pełniejszego wdrażania założeń Przemysłu 4.0. Wschodzące gałęzie przemysłu mogą osiągać nowe poziomy wzrostu i zwinności operacyjnej w dużej mierze dzięki cyfryzacji, która umożliwia wdrażanie elementów inteligentnej produkcji i przyspiesza transformację biznesu przy udziale technologii.
Z jednej strony mowa o systemach automatyzacji, które zwiększają produktywność i wydajność przy jednoczesnej redukcji kosztów. Z drugiej zaś o szerszym podejściu, zakładającym zwiększone przenikanie się technologii informatycznej i operacyjnej (IT/OT), do zagadnienia zmiany w produkcji, jakim jest transformacja z udziałem technologii. Przejście od ręcznych, lokalnie obsługiwanych procesów (jak np. ręczna obsługa i samodzielne monitorowanie kotłów) do zdalnie kontrolowanych procesów sterowania oprogramowaniem (z wykorzystaniem kotła podłączonego do Internetu, powiązanego z innymi procesami) pomoże nie tylko zwiększyć efektywność operacyjną, ale również wpłynie na optymalizację całego zakładu.
Trzecia strona jest związana ze wspomnianą już planowaną przez Ministerstwo Rozwoju, Pracy i Technologii ulgą na automatyzację i robotyzację, która – za sprawą możliwości odliczenia przez przedsiębiorcę od podstawy opodatkowania do 50 proc. kosztów poniesionych na inwestycję – pozwoli na optymalizację kosztową planowej cyfrowej zmiany.
Firmy z sektora produkcji, pozostając przy tradycyjnych systemach, które nierzadko są ich autorskimi rozwiązaniami, ponoszą wysokie koszty dostosowania, modernizacji i integracji z systemami innych dostawców. Dzieje się tak głównie z powodu przestarzałej technologii. Zdolność do osiągania wydajności na tym polu zależy w dużej mierze od umiejętności i wiedzy specjalistycznej w ramach ograniczonych zasobów dostępnych do rozwoju aplikacji i systemów na własną rękę – mówi Tomasz Sierpiński, menedżer sprzedaży w Schneider Electric.
Firmy, które z pełną odpowiedzialnością myślą o przyszłości i wychodzą naprzeciw potrzebom odbiorców, poszukują zróżnicowanych rozwiązań działających w zdecydowanie bardziej otwartym środowisku, w którym integracja nowych aplikacji jest prosta i opłacalna. Tego typu „otwarte” systemy pozwalają na szeroki wybór opcji usprawniania procesów, ułatwiając optymalny wybór rozwiązań w całym cyklu życia produktów. Przykładowo firmy z rozwijających się obszarów poszukują łatwej łączności z systemami MES czy ERP i możliwościami, które przynosi Internet rzeczy (IoT), ale także efektywnej kosztowo integracji z inteligentnymi komponentami sterowania silnikami (MCC), napędami o zmiennej częstotliwości (VFD) czy systemami zarządzania energią i aparaturą obiektową.
Rozszerzający się obecnie zakres cyfryzacji wykracza daleko poza rozproszony system sterowania (DCS) dla głównych procesów. Typowa instalacja procesowa w perspektywicznych segmentach przemysłu musi integrować zbiorniki magazynowe surowców, zbiorniki pomiarowe, reaktory, mieszalniki, miksery, suszarki, wirówki, zbiorniki półproduktów (produktów gotowych), systemy piggingu, systemy transportu pneumatycznego, płuczki, przenośniki czy roboty z operacjami procesowymi – jak załadunek i przenoszenie surowców, kontrolowanie, suszenie, napełnianie itp.
Typowe wyposażenie użytkowe obejmuje z kolei kotły, podgrzewacze cieczy termicznych, wieże i agregaty chłodnicze, stacje uzdatniania wody, sprężarki, oczyszczalnie ścieków i inne. Wiele z tych maszyn jest dostarczana przez wyspecjalizowanych producentów OEM (Original Equipment Manufacturers) i posiada własne systemy automatyki. Aby inwestycje w cyfryzację przełożyły się na konkurencyjność na rynku, wzrost i rentowność, konieczna jest integracja różnych systemów automatyki z centralnym systemem DCS.
Dlatego właśnie np. Schneider Electric opracował produkty DCS nowej generacji, w tym elastyczny system EcoStruxure Process Expert (EPE), a także narzędzia cyfrowe zaprojektowane z myślą o dynamicznym podejściu do procesów inżynieryjnych i operacji. Tego typu rozwiązania umożliwiają nie tylko poprawę efektywności działania przedsiębiorstwa, ale również pozwalają zwiększyć zyski poprzez skrócenie czasu potrzebnego na wprowadzenie produktu na rynek, ograniczenie nieplanowanych przestojów czy ograniczenie zużycia energii elektrycznej nawet o jedną trzecią.
Dziękujemy za przeczytanie artykułu!
Pamiętaj, możesz oglądać naszą telewizję na wPolsce24. Buduj z nami niezależne media na wesprzyj.wpolsce24.